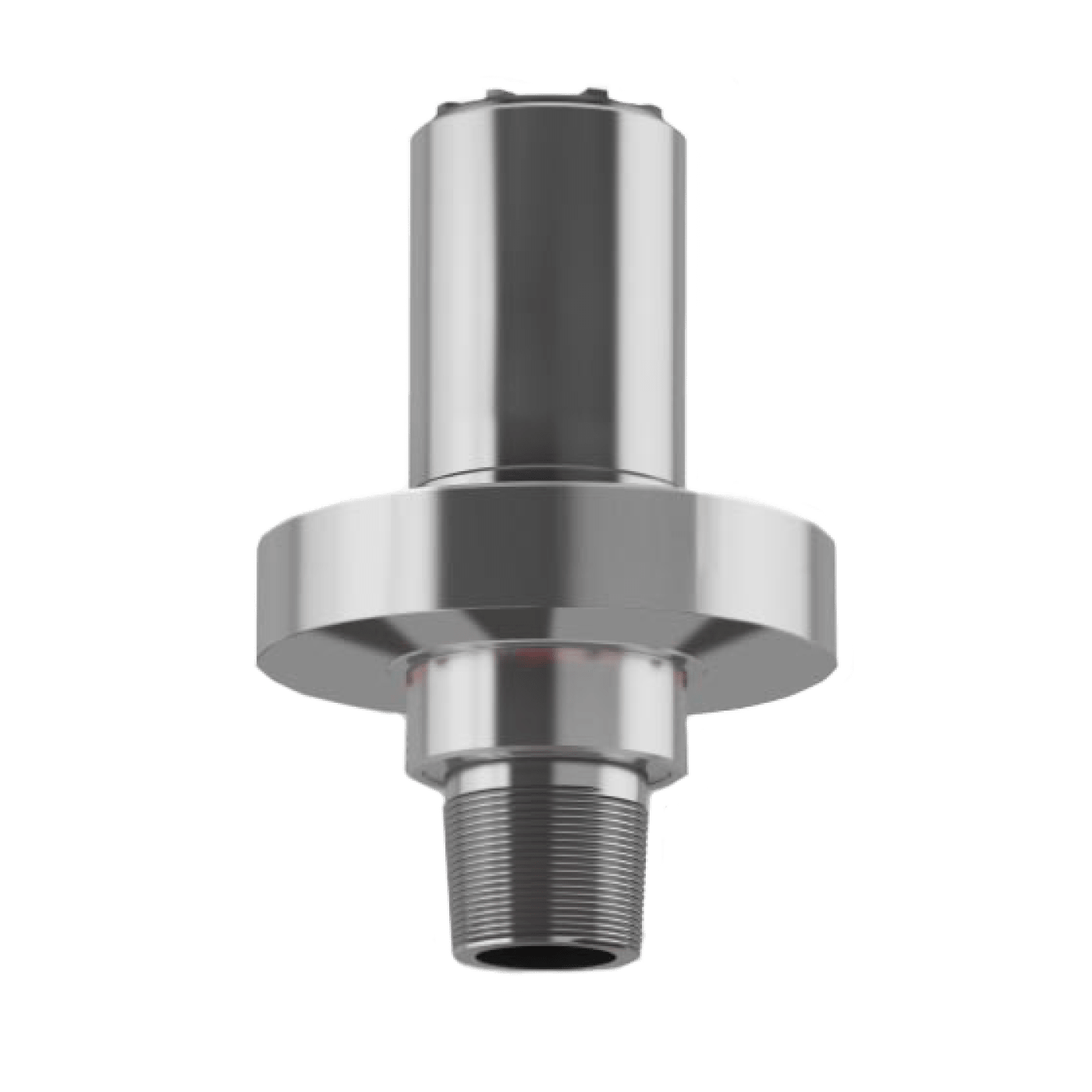
REAL-TIME DRILLING DATA (TTS)
The TTS Sub is installed onto the top drive and designed to measure torque, tension, RPM, pressure and 3D acceleration directly at the drill string. This eliminates algorithm, downhole survey, hydraulic/electronic and shear friction data errors. The sub delivers real-time data and improves reactive assessment of the drilling conditions.
#RedefineTRS™
TORQUE & DRAG ANALYSIS
The TTS can measure reactive torque of a down-hole mud motor when the top drive is not rotating or providing torque readings. Torque can be monitored while drilling in the horizontal section of directional wells. The high speed/high-resolution tension measurements enable precise and efficient auto-driller controls.
TTS data provides early detection of down-hole problems and conditions such as stick-slip, stuck pipe, high mechanical specific energy (MSE), and excess hole drag. For example, extreme stick-slip can destroy drilling bits and cause lost drill strings due to backed-off connections.
The TTS can be equipped with additional sensing capabilities for bending and shear to diagnose and solve quill damage issues due to top drive alignment problems. Torque and tension data measurements use multiple strain gauges distributed evenly around the core to compensate for off-axis loads such as bending.
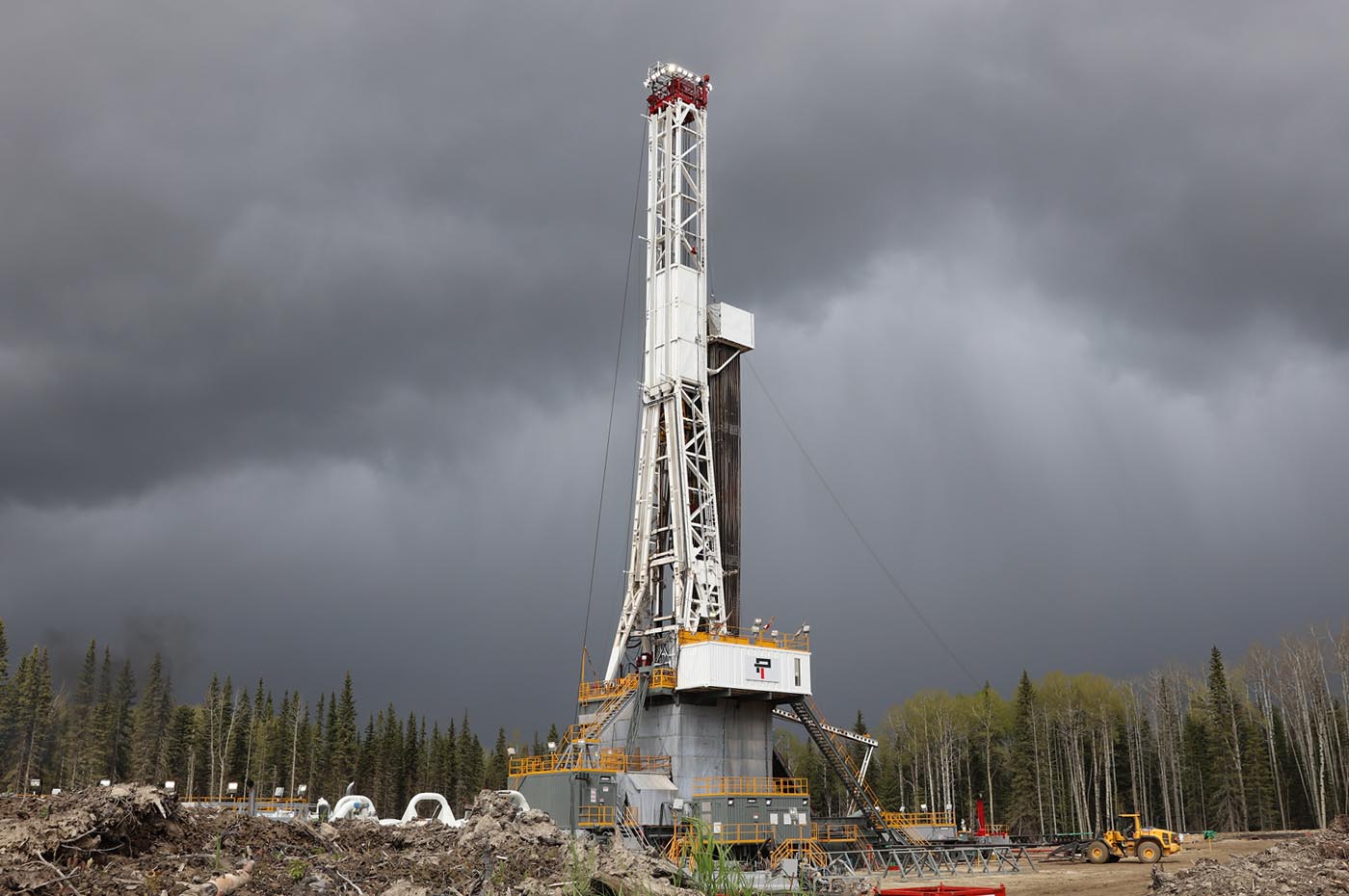
TTS SPECIFICATIONS
Heading #3 | Heading #3 |
---|---|
THREAD ORIENTATION | Pin Up – Box down or Box Up – Pin Down |
TORQUE HOOK LOAD | 40,000 – 80,000 ft/lbs (54,200 – 115,250 Nm) |
TORQUE/TENSION | 350 – 690 ton |
ACCURACY | ±0.5% of Full Scale / ±1% of Full Scale |
TURNS RESOLUTION | ±0.001 Turn Resolution, CW and CCW. 40 RPM Max |
TEMPERATURE RANGE | -40°C to 65°C (149°F) |
BATTERY LIFE | 480 hours at 25°C (77°F) (Approx. 20% lower at 0°C [32°F])
|
WIRELESS TRANSMISSION | 2.4 GHz, Direct Sequence Spread Spectrum /
Line of Sight: Range 150 ft |
ENCLOSURE RATING | Type 4X, Watertight |
HAZARDOUS AREA | North America Class 1, Division 1 Groups
C & D, T4 ATEX: Zone 1, llB, T4 |
DESIGN | Designed to API 8C Certification |
WEIGHT (APPROX.) | 184 – 238 lbs (84 – 108 kg)
|
LENGTH | 24 – 30” (609.6 – 762 mm) |
3D ACCELERATION
Used to record and measure acceleration, the ProTorque® TTS can be equipped to measure pump pressure to 5,000 psi, RPM to 250 rev/min and 3 axis XYZ acceleration to ± 70 g. It’s designed with two independent measurement channels for redundancy in critical applications or to provide additional measurements. Each channel transmits on a different RF frequency to help avoid rig interference issues and range-tested to 1200 feet.
ALL SERVICES, ALL LOCATIONS
CONTACT US TODAY