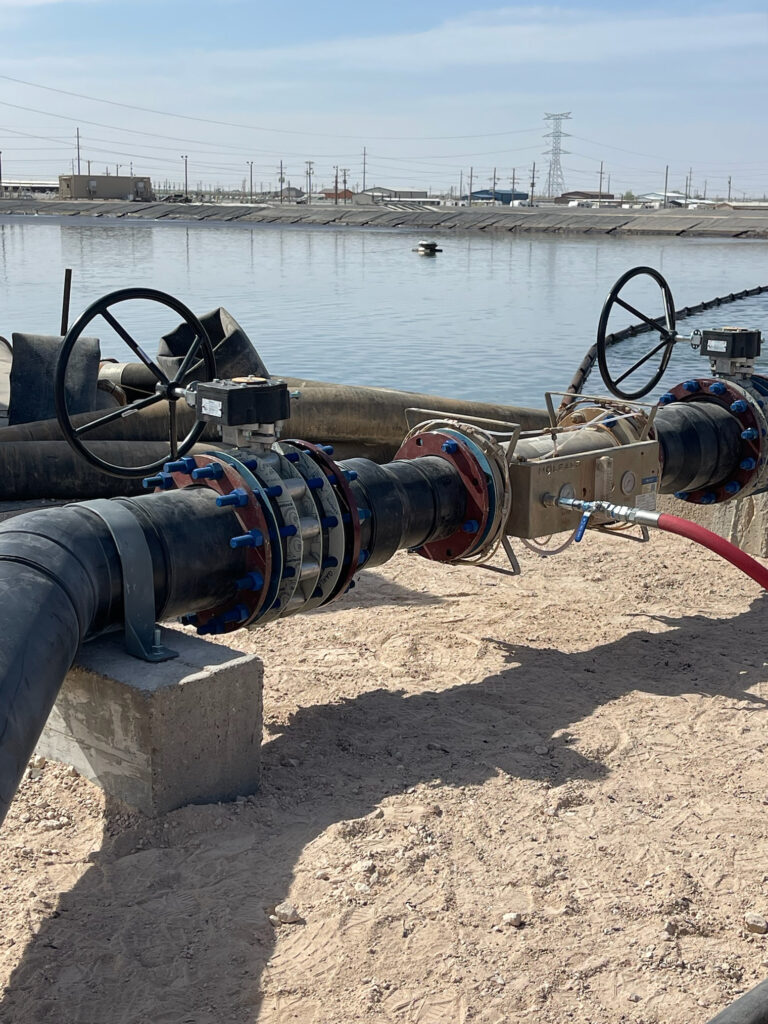
MIDSTREAM SERVICES: EXPERIENCE, SAFETY, AND INNOVATION IN ACTION
ProTorque Energy Midstream (PTEM) delivers integrated midstream solutions rooted in deep experience, current digital practices, and a steadfast safety culture. From pipeline construction and facility maintenance to innovative produced-water recycling, our approach prioritizes operational excellence. We focus on informing and delivering value through technical expertise and proven practices, ensuring safer operations, lower risks, and reliable performance for our partners. Below, we outline how PTEM combines decades of industry know-how with modern technology and training to achieve superior outcomes.
TECHNICAL EXPERTISE AND PRECISE EXECUTION
PTEM’s leadership and crews bring decades of hands-on experience across multiple oil and gas basins. This extensive project background enables efficient execution and meticulous planning, which translates into reliable results for facility owners and operators. Our senior project managers and field supervisors apply deep practical knowledge to every project. For example, we detail complex piping systems and produce accurate, field-ready isometric drawings in-house, streamlining project timelines and reducing costly engineering iterations. The result is fewer delays and “surprises” during construction, keeping projects on schedule and on budget.
Specialized Capabilities: PTEM offers a full suite of midstream construction and maintenance services, leveraging specialized skills and certifications:
- Turnkey Facility Construction: We handle projects end-to-end – from initial site preparation through civil, mechanical, and electrical work – to deliver fully integrated facilities ready for operation.
- 24/7 Pipeline and Facility Maintenance: Our rapid-response maintenance teams provide around-the-clock support to keep pipelines, gathering systems, and plants running smoothly, ensuring consistent uptime and operational continuity.
- High-Quality Pressure Welding: We maintain ASME and API-certified welders for critical infrastructure. Our expert welding ensures the integrity and safety of pipelines and pressure vessels, meeting strict industry standards.
Midstream project execution often involves heavy machinery and skilled coordination. PTEM’s experienced crews and certified specialists ensure that construction and maintenance tasks are performed safely and efficiently, minimizing downtime.
This breadth of capabilities means fewer third-parties and handoffs, giving clients a single accountable partner for midstream projects. Our depth of expertise, combined with careful planning, delivers tangible benefits – less downtime, fewer costly surprises, and consistently high-quality results for our customers.
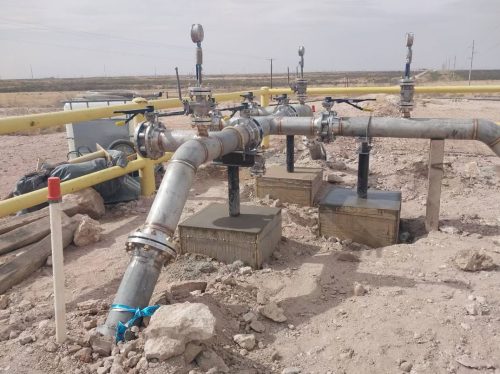
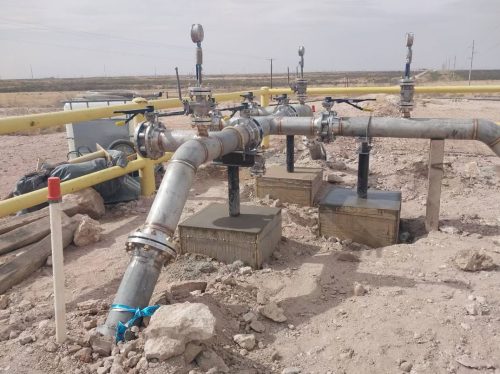
DIGITAL WORKFLOWS FOR EFFICIENT MAINTENANCE
Midstream maintenance demands rapid response and accurate execution. PTEM has embraced digital transformation to meet these demands. We moved away from traditional paper-based processes by implementing tablet-based digital workflows across all field maintenance activities. Field technicians now capture job data, equipment checklists, and safety observations on mobile devices, enabling real-time communication between the field and office. This connectivity yields several key advantages:
- Instant Data Sharing: Work details (e.g. completed inspections or repairs) are synced instantly, leading to faster and more accurate job estimates and decision-making.
- Improved Visibility: Office and management personnel can track job progress in real time, which streamlines communication and allows proactive support or adjustments as needed.
- Reduced Administrative Burden: Digital records are automatically saved and organized. Instead of shuffling paperwork, teams can retrieve maintenance history, reports, and safety documentation immediately, accelerating approvals and reducing delays.
These digital workflows do more than save time – they improve reliability. By having up-to-date data at hand, our maintenance planners can schedule preventive actions more effectively, catch issues earlier, and avoid repeat trips. Industry studies have found that fully digitizing maintenance processes can increase equipment uptime by 5–15% and cut maintenance costs by 18–25%, thanks to gains in data-driven planning and reduced errors. PTEM’s on-the-ground experience reflects these gains: by using connected apps for inspections and reporting, we minimize miscommunication and ensure that no detail falls through the cracks. The bottom line is safer, faster maintenance that keeps critical midstream assets online.
SAFETY EMBEDDED IN EVERY OPERATION
At PTEM, safety is integrated into everything we do. We recognize that midstream construction and maintenance involve inherent risks, so we take a proactive, systematic approach to safety management on every job site. Key elements of our safety program include:
- Daily Job Safety Analysis (JSAs): Each day and for each new task, crews perform JSAs to identify potential hazards and mitigation steps. This habit ensures everyone starts the job with situational awareness and clear safety controls.
- Dedicated Safety Supervisors: For critical or high-risk projects, we assign experienced safety officers to oversee operations in the field. Their presence reinforces safe work practices, conducts spot inspections, and empowers any worker to pause work if unsafe conditions arise.
- Rigorous Equipment Inspections: All tools, lifting gear, and heavy machinery undergo regular inspections and maintenance. Preventive upkeep of equipment helps avoid malfunctions that could lead to accidents.
By embedding these practices, PTEM has significantly reduced the risk of incidents, protecting our crews and clients’ assets. Our safety protocols not only prevent injuries but also avoid unplanned downtime or environmental incidents that can result from accidents. This integrated safety culture maintains client trust and ensures projects stay on track.
Importantly, safety at PTEM goes hand-in-hand with performance. We believe that a safe operation is an efficient operation. Industry data supports this: companies with strong safety training and culture have far fewer accidents. Comprehensive safety programs can cut workplace injuries by up to 50%. Fewer incidents mean work isn’t interrupted by investigations or manpower loss, which in turn means higher productivity. Our clients benefit from this safety-first ethos through peace of mind and reliable execution: jobs are done right the first time, without the setbacks that accidents or compliance issues can cause.
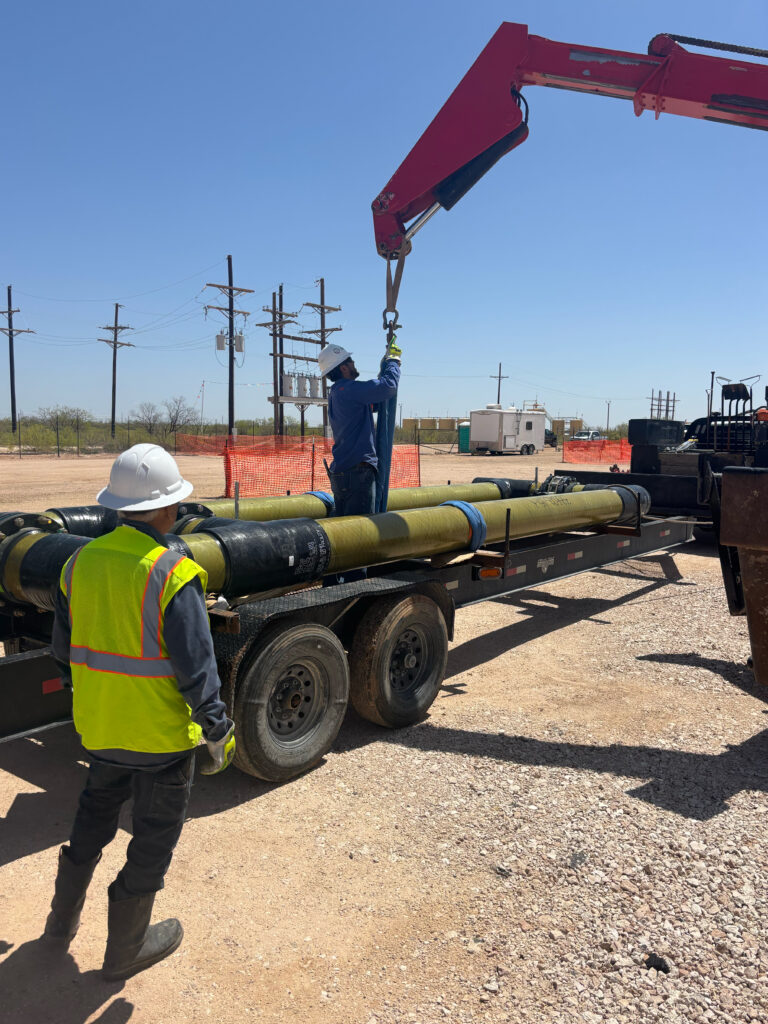
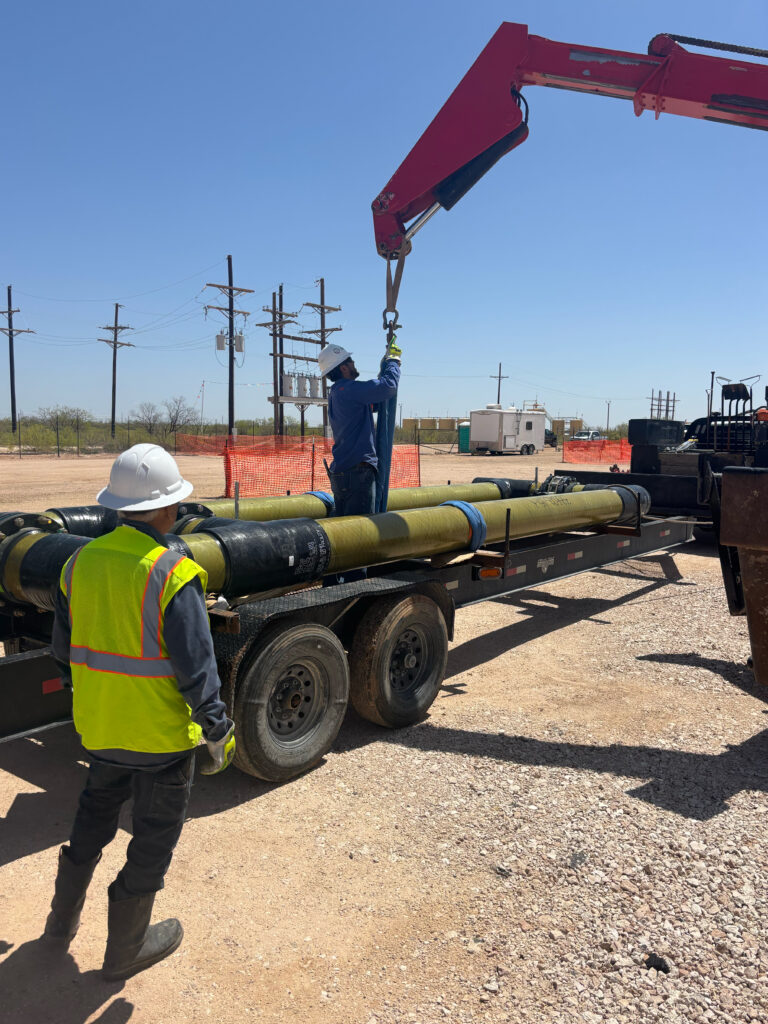
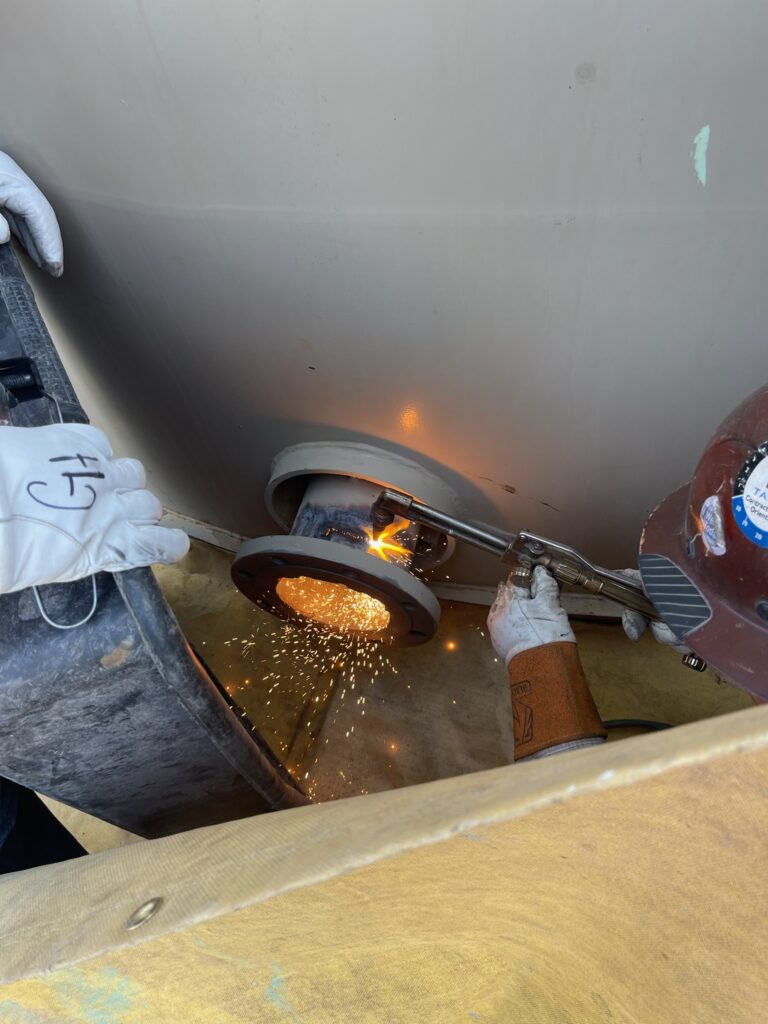
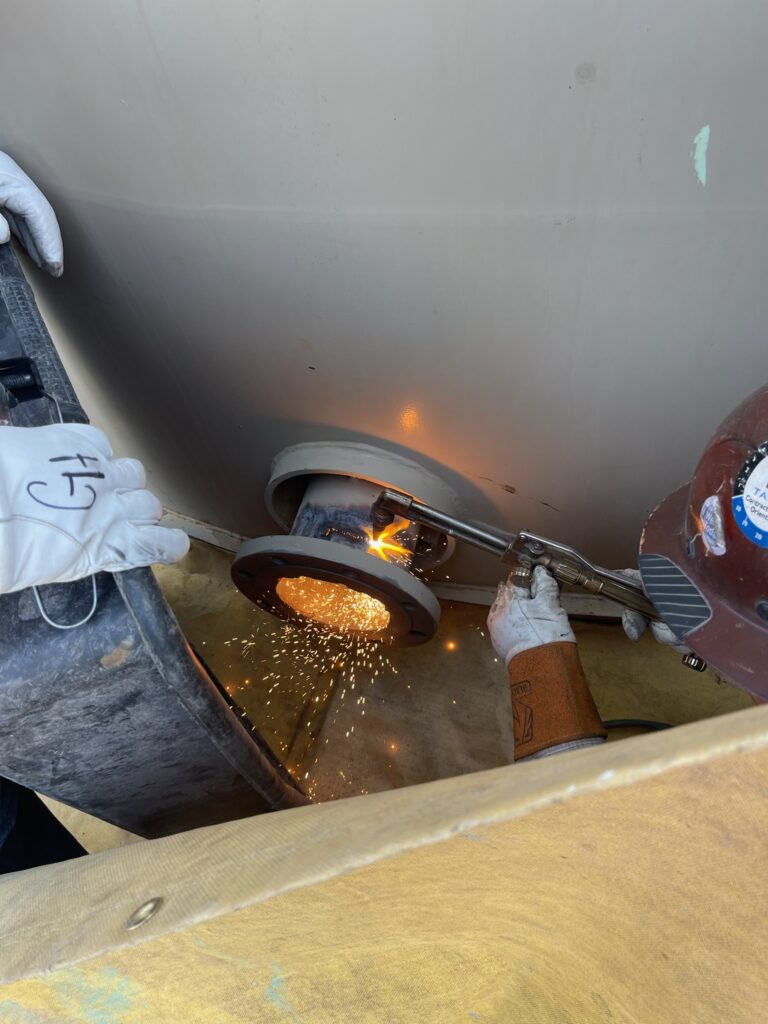
CONTINUOUS TRAINING AND DEVELOPMENT
To maintain our high safety and quality standards, PTEM heavily invests in ongoing training for all team members. We operate a dedicated training center that provides structured, scenario-based instruction replicating the challenges of midstream field work. This goes beyond basic orientation – it’s a continuous program to sharpen skills and verify competencies:
- Hands-On Simulations: Employees regularly practice high-risk tasks in controlled environments. For example, crews might simulate a pipeline tie-in or pressure test procedure, allowing them to refine their technique and response to unexpected issues in a safe setting.
- Certifications and Skill Mastery: We ensure every worker is fully certified and competent for the jobs they perform. Welders go through ASME/API certification programs and must demonstrate their ability on test joints. Electricians and instrumentation techs train on the latest automation systems. This rigorous preparation means our people show up to the job ready to execute correctly and safely.
- Safety Drills and Compliance: Safety training is continuous. Workers review and drill on emergency response, proper use of personal protective equipment, and new safety protocols. By reinforcing these practices, we cultivate second-nature safety habits across the team.
This training-driven approach directly leads to superior operational discipline in the field. Teams that have repeatedly practiced tasks are more efficient and less prone to error. They are also more adaptable – if an unforeseen situation arises, a well-trained crew can draw on their exercises to respond effectively rather than react in panic. The payoff for our clients is tangible: fewer safety incidents, greater reliability, and lower overall risk during projects. In other words, our workforce training is an investment that protects your operations.
Moreover, training in specialized techniques allows us to tackle unique midstream challenges. For instance, PTEM technicians receive extensive education in handling corrosion-resistant materials (like fiberglass reinforced piping and HDPE) used in modern water infrastructure. This expertise leads to longer-lasting installations and fewer unexpected maintenance needs for facilities. By keeping our teams at the forefront of industry best practices, PTEM ensures that we not only meet regulatory requirements but often exceed them, delivering work of a quality that stands the test of time.
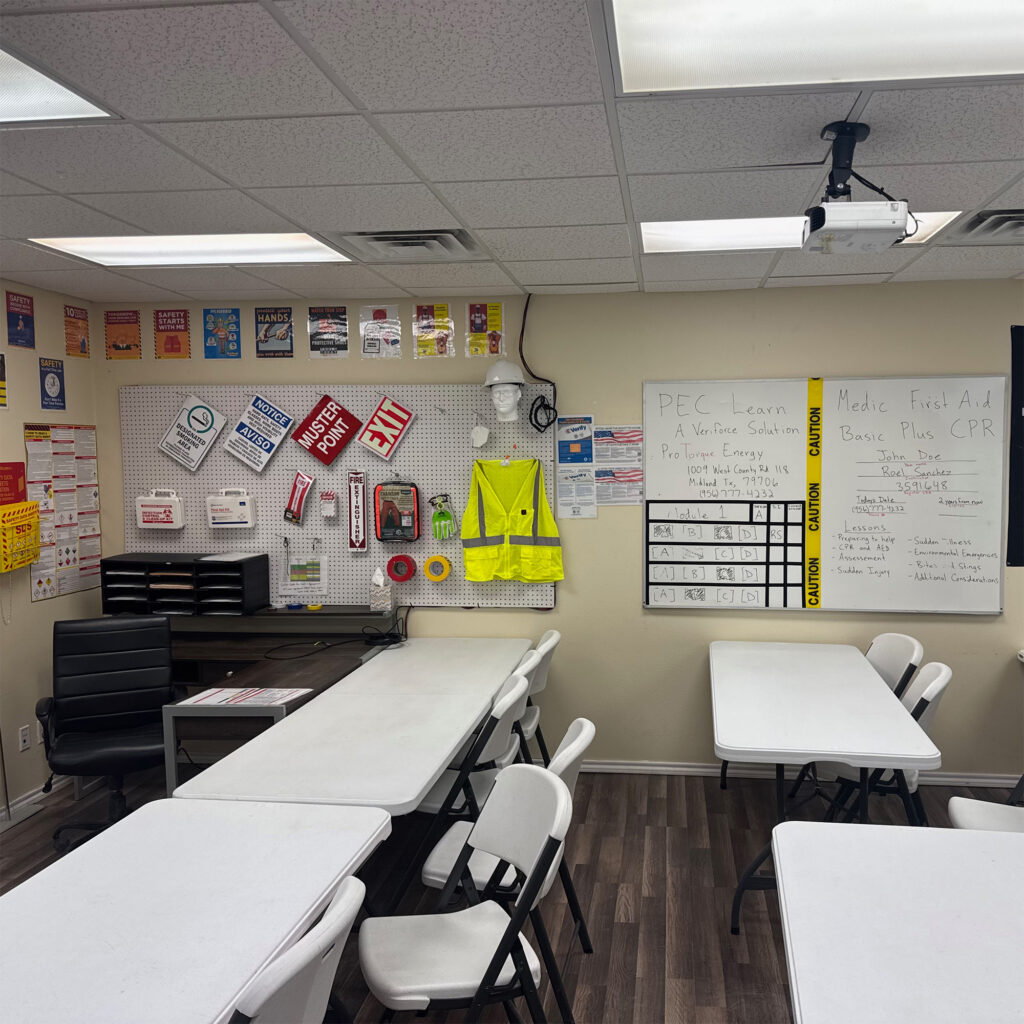
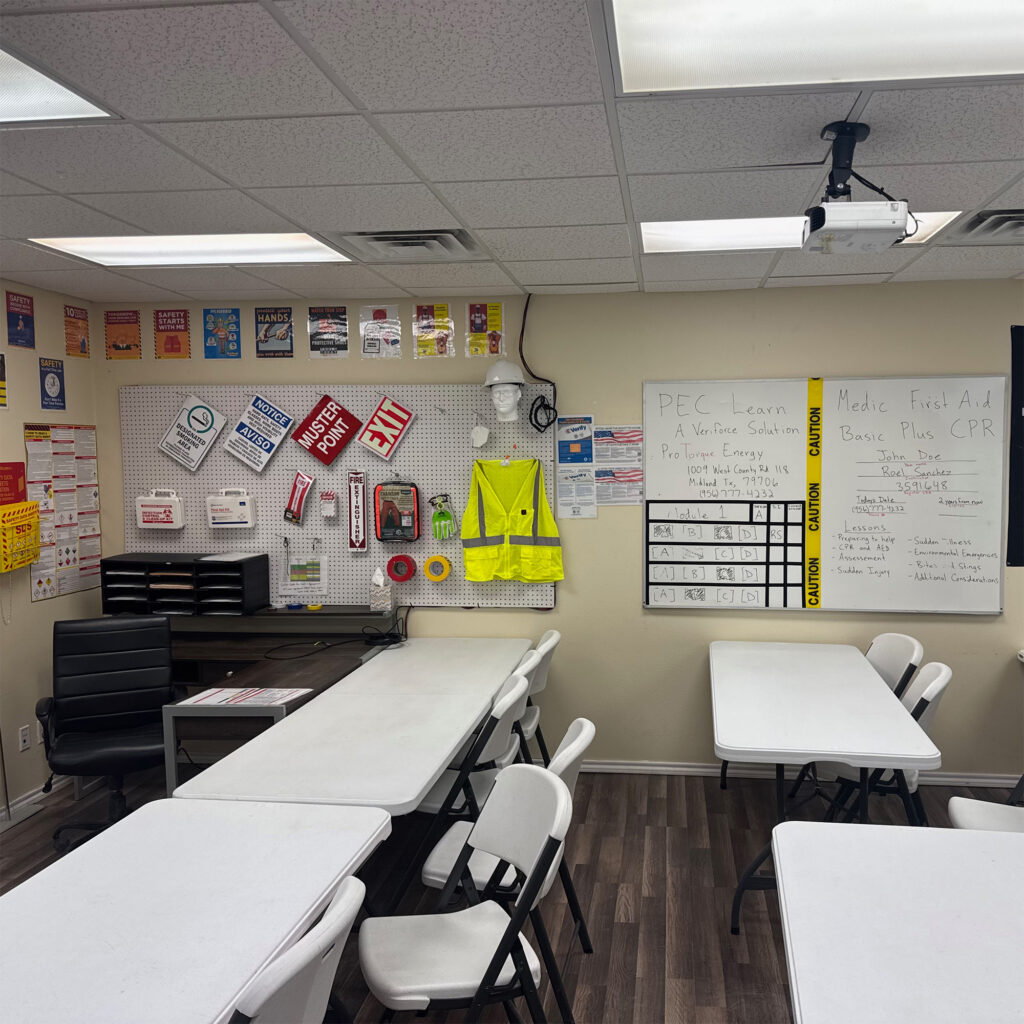
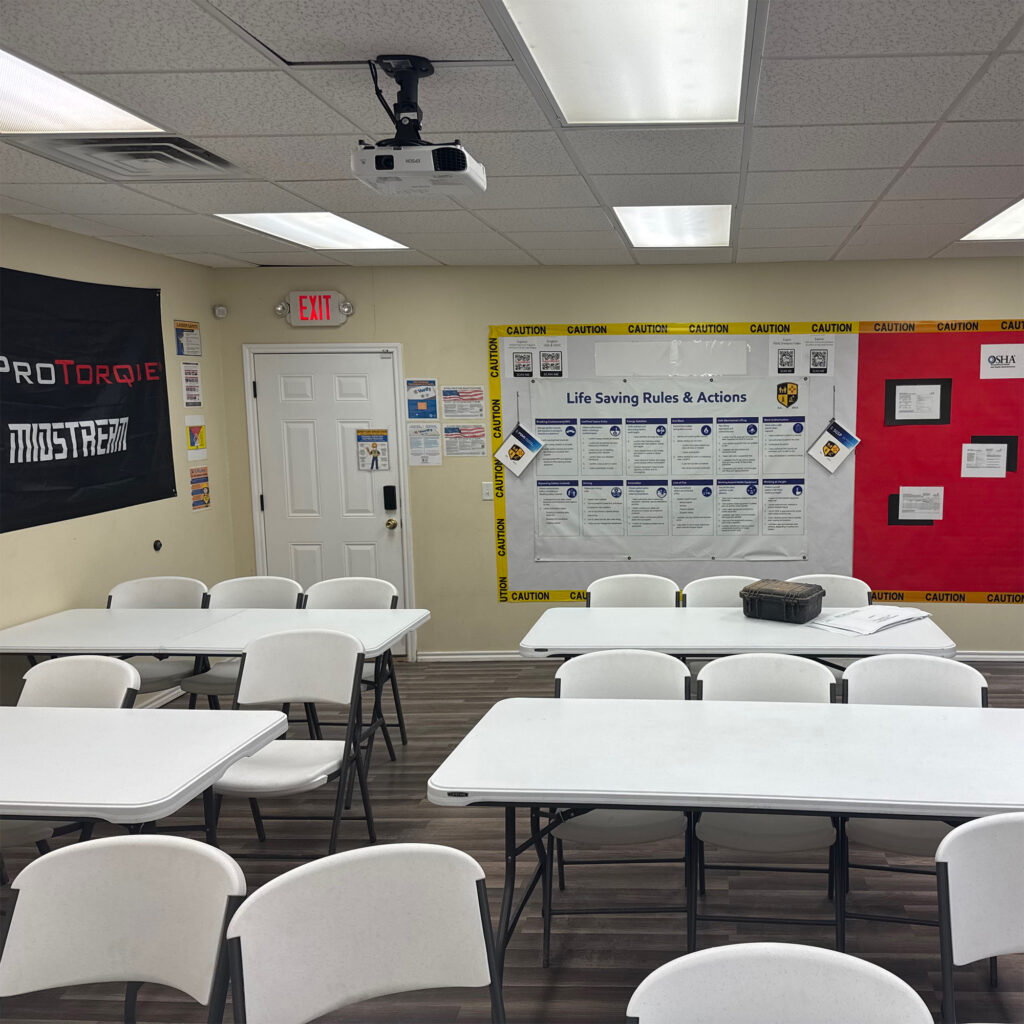
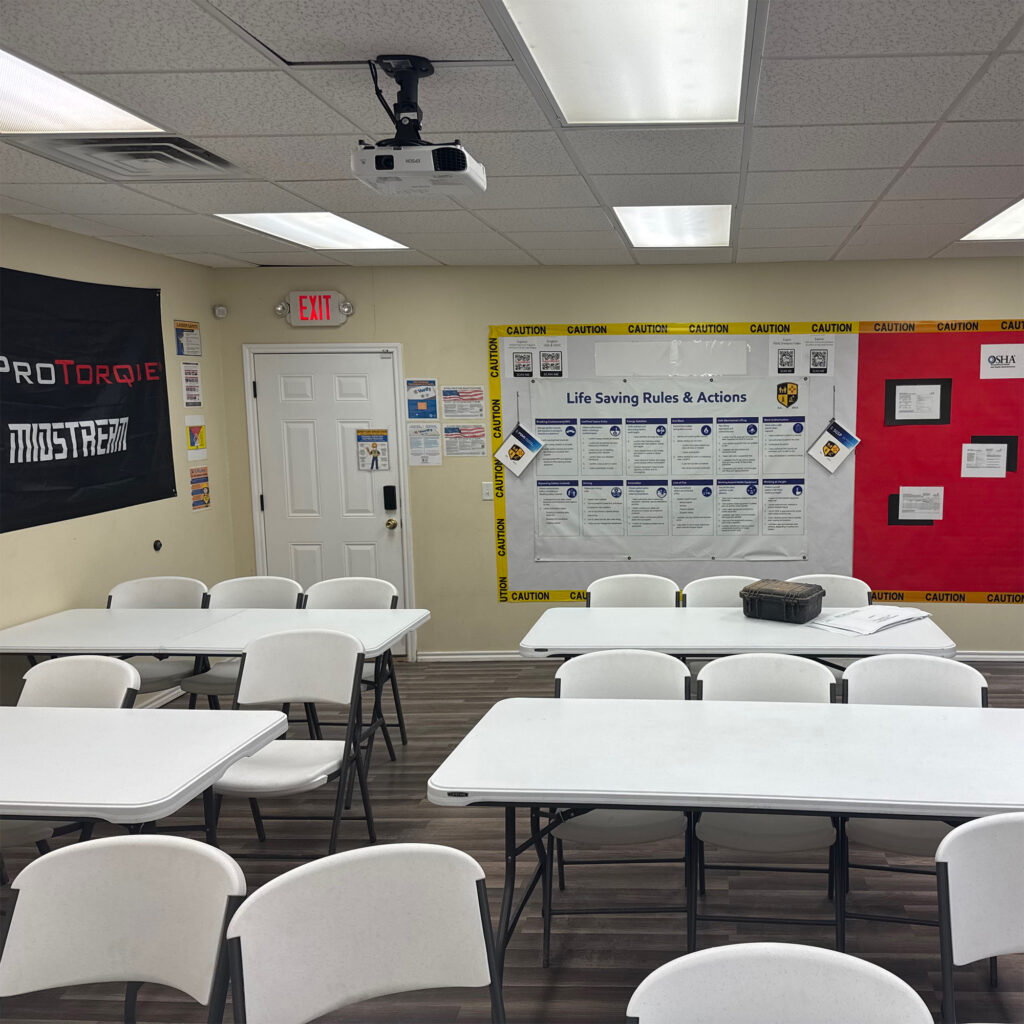
INNOVATIVE WATER MANAGEMENT SOLUTIONS
Produced water management is a pressing operational and environmental challenge in many oil and gas plays. Rather than view it as a burden, PTEM helps operators turn produced water from a liability into an asset. We specialize in the design and construction of Clean Brine Facilities (CBFs) – advanced water treatment installations that enable the recycling and reuse of produced water for hydraulic fracturing and other operations.
Our turnkey approach to CBF projects covers every aspect of water infrastructure. We handle site preparation and containment (including engineered liners and berms), install corrosion-resistant fiberglass pipelines and storage tanks, perform poly fusion welding for leak-proof connections, and integrate state-of-the-art water treatment systems. The goal is to treat the “dirty” produced water so that it meets the quality specifications for reuse in fracturing fluid or other industrial processes. By converting produced water into a reusable resource, operators can dramatically cut both disposal volumes and freshwater procurement. This yields substantial cost savings and environmental benefits – less wastewater to inject underground and less strain on local freshwater sources.
To put the economics in perspective, reusing produced water is often far cheaper than disposing of it. In the Permian Basin, for example, trucking and injecting wastewater can cost anywhere from $0.25 up to several dollars per barrel, depending on distance and disposal fees. In contrast, recycling that water for reuse has been achieved for roughly $0.15–$0.20 per barrel, well below typical disposal costs. That difference can translate to millions saved when you consider the high volumes of water involved. It also reduces the number of truck trips needed (cutting traffic and emissions) and mitigates the risk of induced seismicity linked to massive disposal injection. In short, a PTEM Clean Brine Facility helps clients save money while operating more sustainably. (Source: JPT (Society of Petroleum Engineers) – Balancing Growth and Risk: Water Management in the Permian (2025), on produced water recycling vs. disposal costs)
PTEM has a proven track record in this domain – our crews have successfully delivered multiple CBF projects, particularly across the Permian, tailoring each facility to the operator’s water composition and volume needs. Our experience allows us to anticipate site-specific challenges (such as scaling, bacterial growth, or variable water chemistry) and address them in the design phase. We also ensure a smooth startup and integration with the client’s existing infrastructure, so the new facility ramps up to full operation quickly and reliably.
Finally, as mentioned, our specialized training on these water systems means the teams building and maintaining your water treatment equipment are highly knowledgeable. They adhere to best practices for chemical handling, pump maintenance, and instrumentation calibration on water treatment units. The result is longer equipment life and more uptime for the water facilities, directly contributing to higher overall field productivity. By embracing practical innovation in water management, PTEM helps clients transform produced water from an operational headache into a strategic advantage.
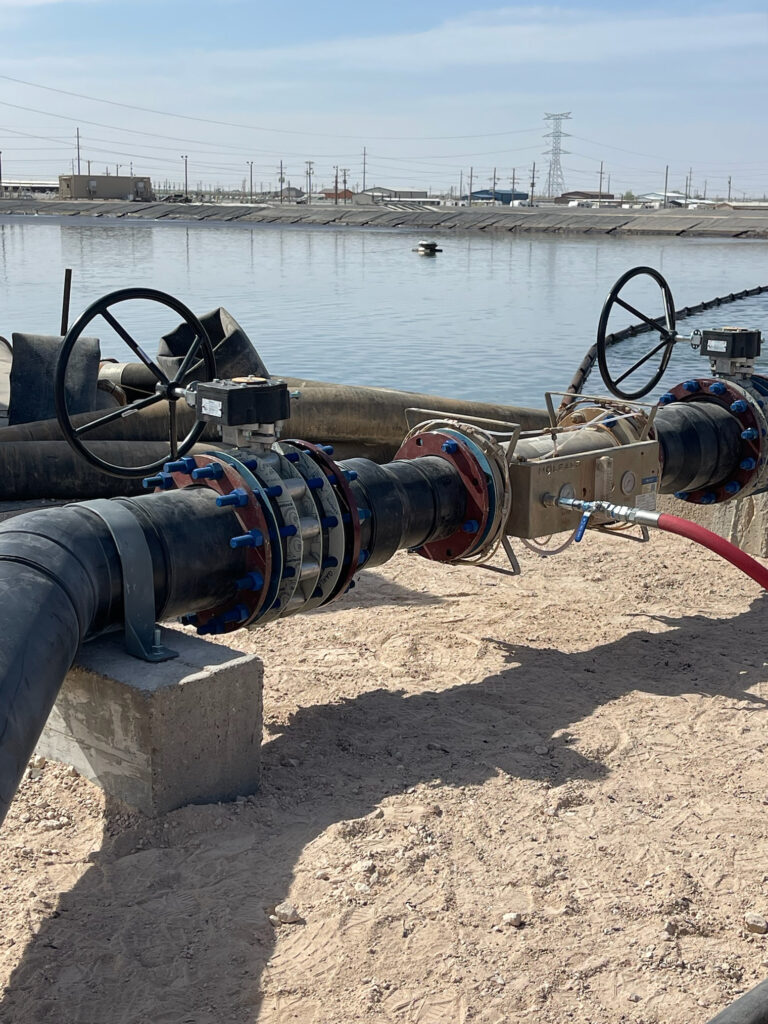
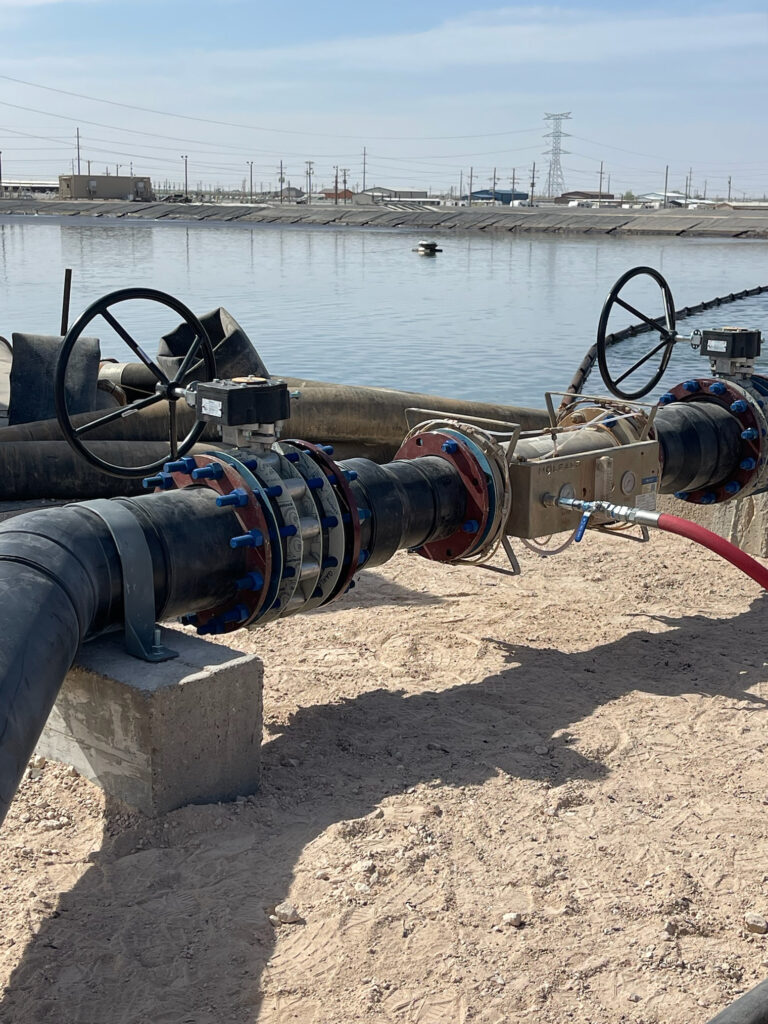
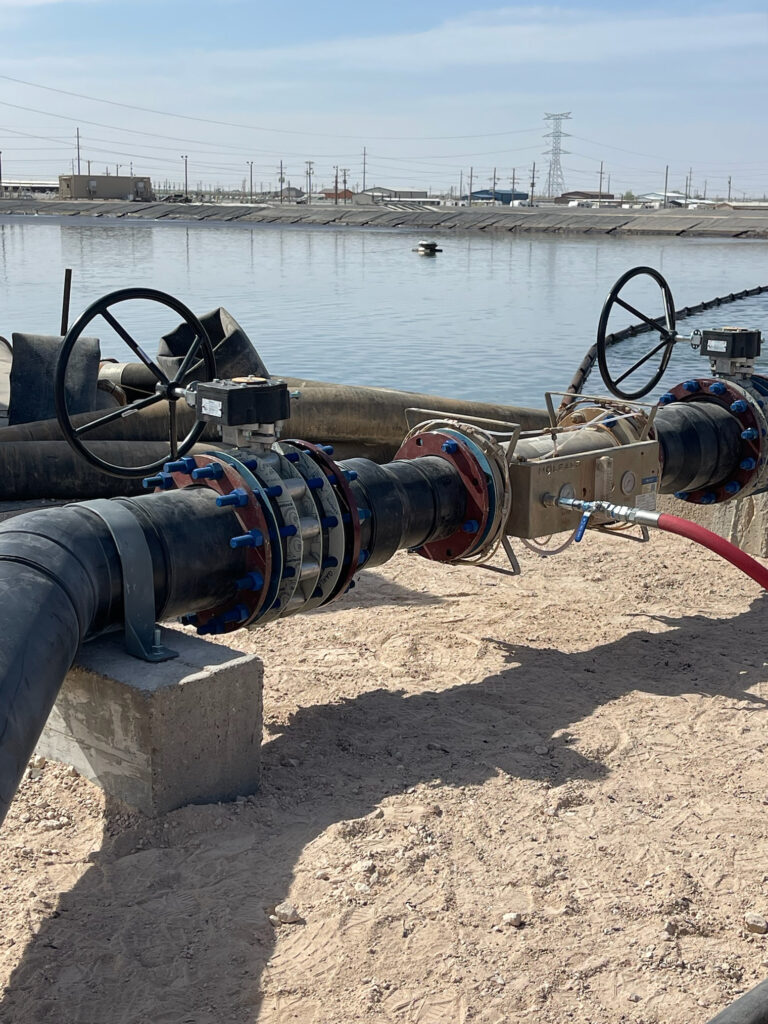
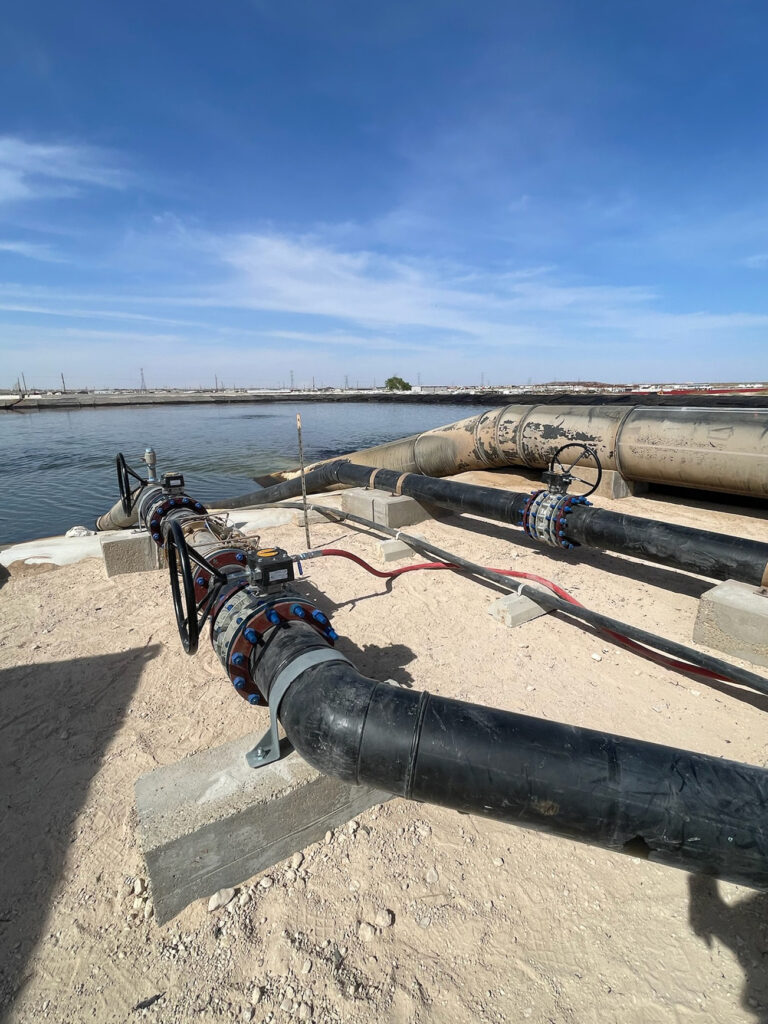
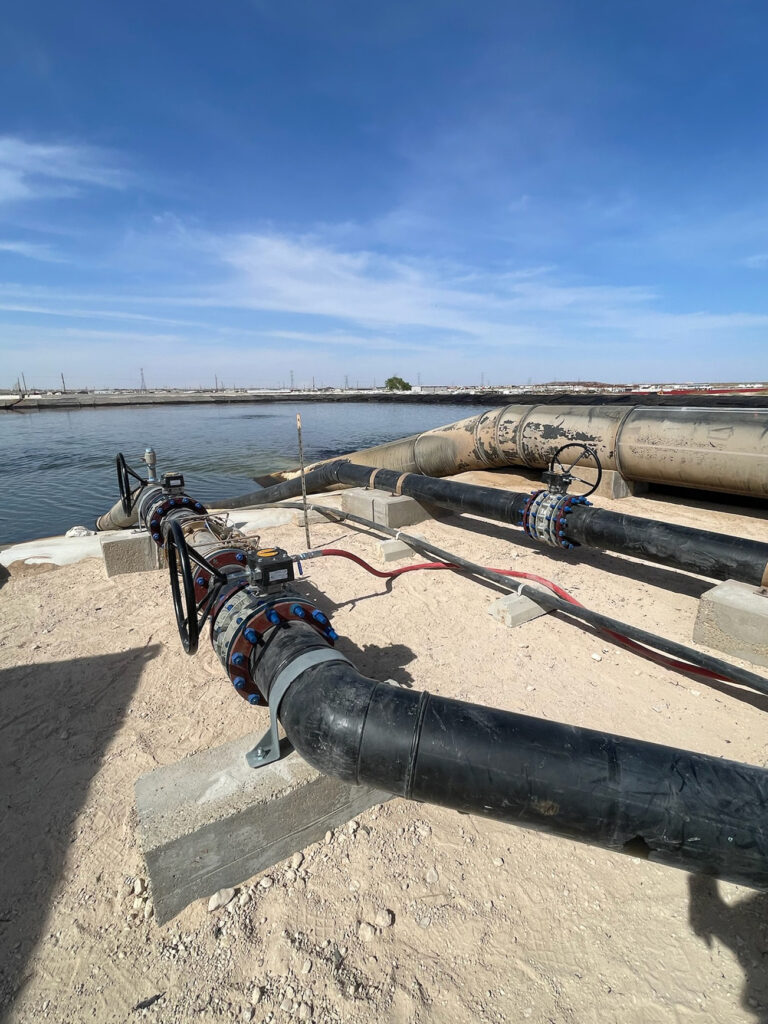
DELIVERING RELIABLE VALUE FOR MIDSTREAM OPERATIONS
By combining digital efficiency, rigorous safety standards, experienced personnel, and continuous training, ProTorque Energy Midstream consistently delivers dependable results for midstream operations. Our approach is about proven practices that yield real value:
- Fewer Disruptions: Careful planning, preventive maintenance, and quick response keep unplanned downtime to a minimum. Clients can trust that their pipelines and facilities will operate smoothly with PTEM on call.
- Safer Job Sites: A strong safety culture and skilled crews mean projects are completed without incident. This protects everyone involved and avoids the cascading delays and costs that come with accidents.
- Strategic Partnerships: We see ourselves as a partner in our clients’ success. Whether it’s protecting assets through proper maintenance or innovating a solution for water reuse, we align our services with the client’s operational goals. Your success is our priority, and that ethos guides every decision.
PTEM’s midstream services deliver operational reliability and peace of mind. Backed by decades of expertise and a forward-looking adoption of technology, we help midstream operators and facility owners achieve their objectives efficiently and safely. Our experience means you can count on us for honest assessments, fit-for-purpose solutions, and execution excellence.
EXPLORE OUR LATEST MIDSTREAM INSIGHTS
For a deeper dive into how PTEM approaches midstream challenges, check out our recent blog posts:
- Enhancing Midstream Maintenance Through Digitalization and Safety – A closer look at how digital workflows and a safety-first mindset are improving maintenance outcomes.
- Expertise and Precision: Our Approach to Midstream Construction and Maintenance – Learn how experience, planning, and training come together to drive project success in midstream operations.
- Clean Brine Facilities: Turning Produced Water into Operational Advantages – Discover how water recycling facilities can cut costs and boost efficiency in produced water management.
COMPREHENSIVE SOLUTIONS
ProTorque Midstream offers a full slate of construction, pipeline maintenance and environmental services delivered safely, efficiently and cost-effectively. Whether you’re seeking an integrated solution or have a specific service need, we’re here to help.
TURN-KEY PROJECTS
- Civil
- Construction
- Pipeline
- Mechanical
- Electrical
- Instrumentation
- Facility
INSTRUMENTATION & ELECTRICAL
- Full-Service Automation
- Instrumentation & Electrical
(programming, tubing, conduit,
installation, maintenance, etc.) - Instrument Calibration
- Plant & Facility Maintenance
CONSTRUCTION
- Saltwater Disposals
- Clean Brine Facilities
- Pipeline Construction
- Pipeline Gathering System
- Plant & Well Site Facilities
- Amine Plants
- DEHY Stations
- Compressor Station
- Well Hook-Ups, Fiberglass, HDPE Pipe
- Full-Service Paint Crews
- Steel Erection & Fabrication
- Site Work – Preparing Drilling Site/Backfilling Reserve Pits, etc.
SAFETY TRAILERS
- Safety Trailers, Eye Wash
& Shower
Equipped
PIPELINE MAINTENANCE
- General Oilfield Maintenance
- Pipeline Repairs Installations &
Rehab on Existing Lines - Pipeline Integrity Digs
- Pipeline Material Supply
- Hot Taps Up to 30” Lines
- Welding/Specialty
- Clearing ROW
- Mowing Crews
- Site Work
- Reclamation
ENVIRONMENTAL SERVICES
- Liners – Reserve Pit & Pad Liners (Smooth and Textured) 20 – 45 mil.
- Temporary Containment Systems
- Environmental Control Products