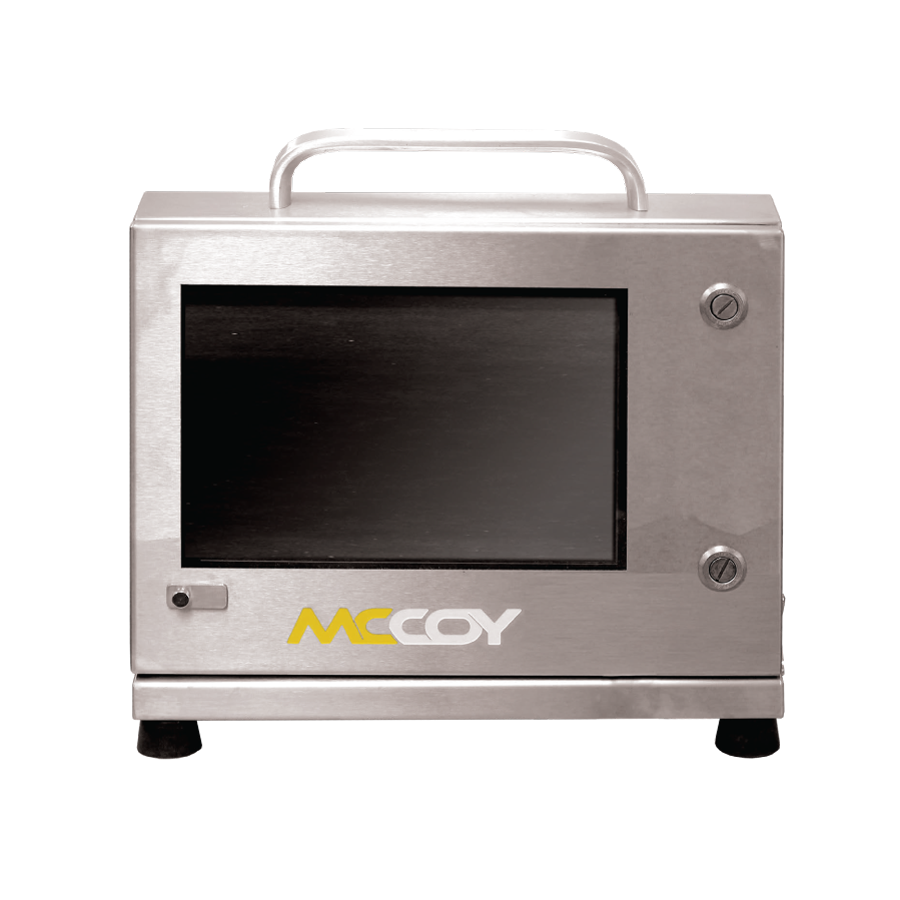
COMPUTER ANALYZED TORQUE MONITORING (CATM) – POWER TONGS
With a variety of issues that could occur while making up an array of different connections on the market, at ProTorque it is our belief that all tubular connections should use computer analysis. CATM delivers a graphical representation that allows us to interpret and prevent damaged or incorrectly made up connections from entering the wellbore. It helps to ensure peak performance and proper isolation for your packer systems. This isolation reduces and helps to eliminate leaks during the fracturing (FRAC) process, in turn mitigating environmental and unforeseen production risks.
#RedefineTRS™
FIELD ACCOUNTABILITY
Connection related issues are stopped immediately, mitigating the risk of further connection damage
Detailed graphical reports are generated highlighting each connection, statistical analysis and summary reports
Reduces damage due to RPM, over-torque, over-rotation and alignment issues
Recording and reporting torque, turns, RPM and applicable shoulder data for semi-premium and premium connections
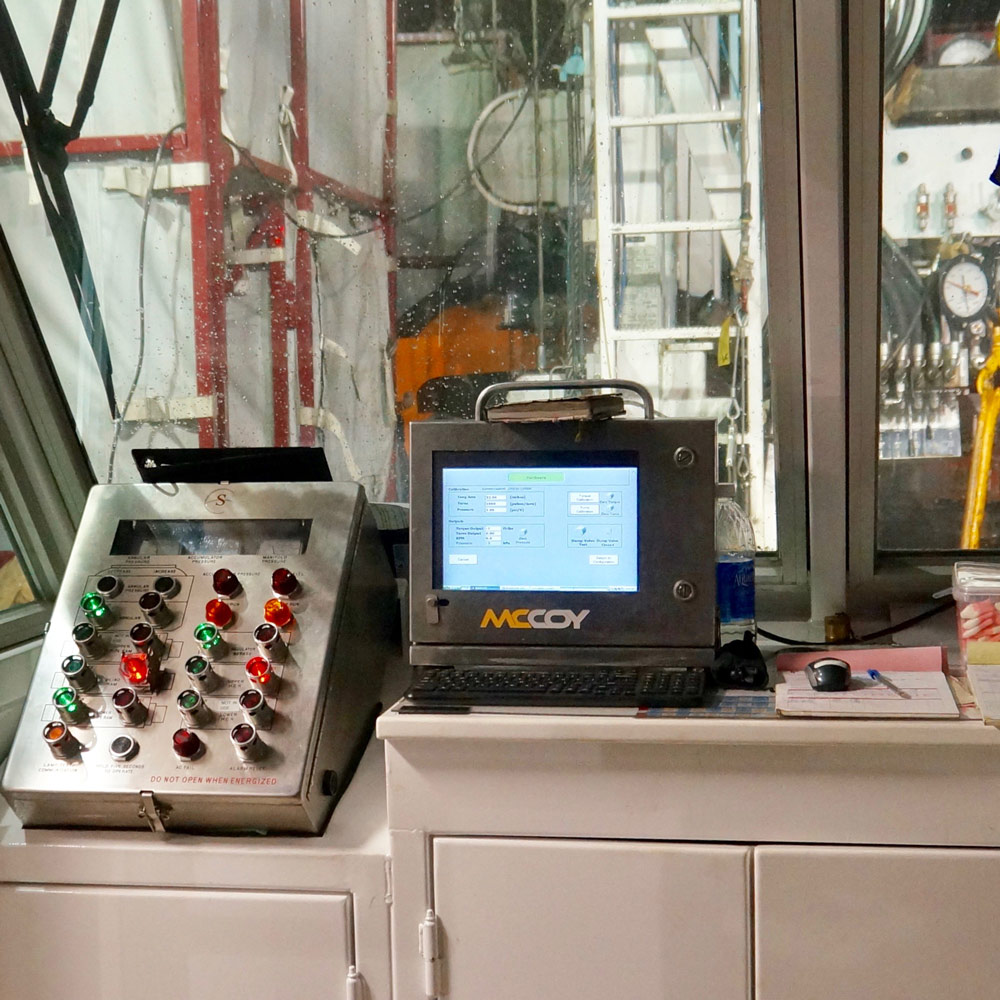
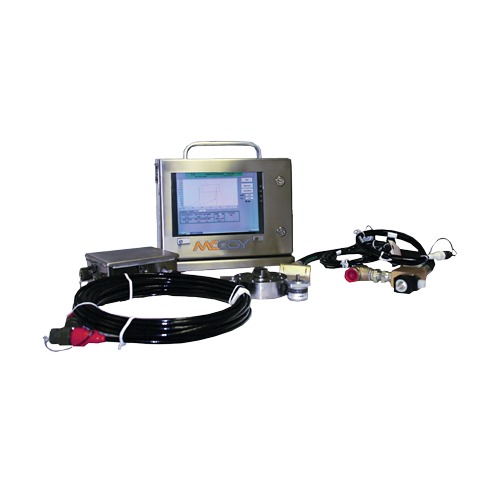
FEATURES
Automatic system review of torque vs turns & time, delta torque and delta turns
Automatic shoulder selection and zoom review for accurately confirming shoulder point before connection approval
Data overlay to ensure consistency of the “last 10” joint review
Sensory control to ensure that the computer analytics can sample and review data correctly, even during challenging runs, conditions and connections
Real-time hydraulic dump control to protect the integrity of the connection
SPECIFICATIONS
Heading #3 | Heading #3 |
---|---|
SAMPLING FREQUENCY | 1 – 8000 Hz |
RECORDING FREQUENCY |
Combined delta torque and delta time |
CAL. MANAGEMENT | Mfg. specifications or local calibration. Shunt calibration with automatic “drift” tracking. |
RESPONSE TIME | Electronics < .5 ms Hydraulic dump valve - typically 10 – 30 ms. |
FINAL TORQUE | Average = optimum torque + – 1% Standard deviation < 2% under normal operating conditions. |
OPERATING TEMP | Computer, 5 – 50°C (40 – 122°F) Junction box, minus 30 – 80°C (minus 22 -180°F) |
TORQUE ACCURACY | Max error (% of full scale) = sqrt [Local force standard error2 + arm length error2 + 0.152] Typically less than 1%. |
TURNS ACCURACY | Max error = + – one pulse of turns counter. |
PRESSURE ACCURACY | Max error (% of F.S.) = sqrt [pressure standard error2 + 0.152] Typically less than 1%. |
ALL SERVICES, ALL LOCATIONS
Contact Us today!